Coaxial Rotor Capstone Project
Project Background:
-
A member of my capstone project team discovered the paper "Geometry Design of Coaxial Rigid Rotor in High-Speed Forward Flight" by Wang et al. that described optimal coaxial rotor planform geometry.
-
The paper detailed parametric equations for the optimal planform geometry but did not produce and test the proposed geometry which appeared to be an opportunity for a cross disciplinary capstone project.
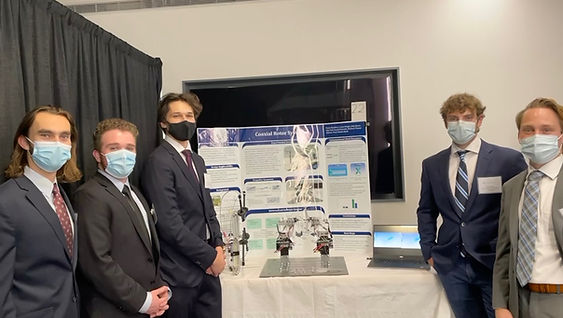
Capstone Team with Final Poster
Project Summary:
-
Design and execute an experiment to test the performance of the proposed optimal coaxial rotor geometry from the Wang et al. paper.
Mechanical Design Steps:
-
Modeled and 3D printed custom geometry suggested by Wang et al. using Solidworks.
-
Assisted CFD analysis of custom geometry using Ansys Fluent and adjusted propeller geometry based off results.
-
Worked with members to design thrust stand and source electrical motors based off mechanical requirements.
Challenges:
-
Modeling the propellers proved to be more challenging than expected due to blade twist.
-
Solidworks was used initially and then put to the side to try NASA's open sourced aircraft component software OpenVSP. However OpenVSP did not have the customization required to achieve the exact planform geometry.
-
Blades were eventually modeled by generating a 3D pointcloud of the blades, with twist, in MATLAB and then importing cross sections to Solidworks for lofting.
-
Results:
-
Both CFD and experimental results showed that linear custom twist geometry had higher thrust per input power than the DJI Phantom 3 (an industry standard single rotor propeller) in both single and coaxial configurations.
-
Our capstone project was selected by external judges to be one of 6 finalists.
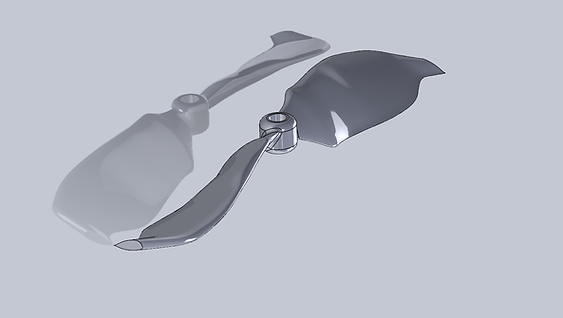
Linear Twist Custom Propeller
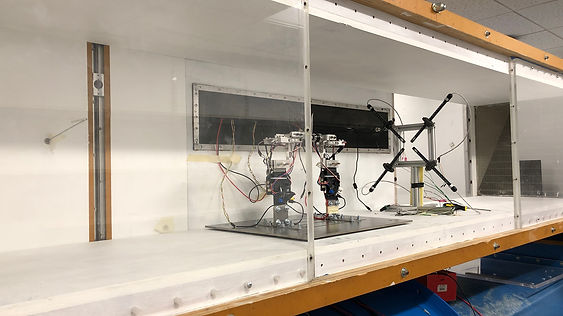
Custom Thrust Test Stand in Wind Tunnel

Theoretical and Experimental Performance Comparison for DJI Phantom 3 and Custom Geometry